Load Bearing Wall Removal
Load Bearing Wall Removal
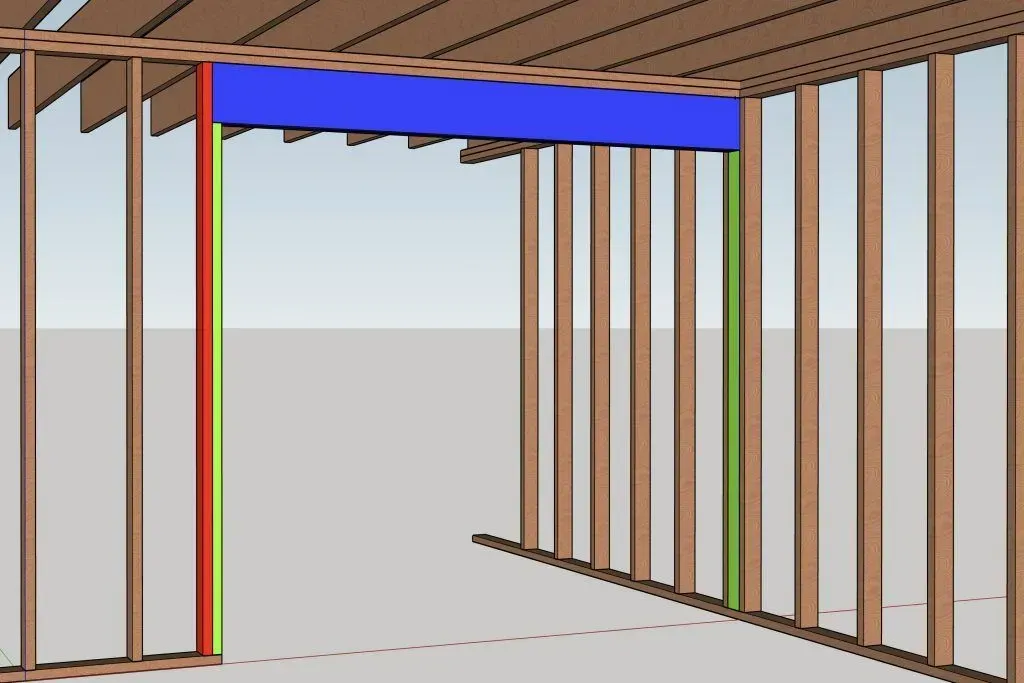
Removing a load-bearing wall in a wood frame structure is a significant undertaking that requires careful planning, proper assessment, and adherence to engineering principles. This article provides a comprehensive guide on how to determine load-bearing walls, perform due diligence, consider engineering provisions, choose appropriate beams, and follow the correct process.
Identifying Load-Bearing Walls
- Understanding Load Paths: Load-bearing walls transfer weight from the roof and upper floors down to the foundation. To identify these walls, understanding the load paths is crucial. Typically, walls parallel to ceiling joists are non-load-bearing, while those perpendicular are load-bearing.
- Blueprints and Building Plans: Reviewing the original building plans can provide insights into which walls are designed to bear loads. Structural walls are usually marked and highlighted in these documents.
- Inspecting the Structure: Physically inspecting the attic or basement can help identify which walls carry the weight of the structure. Look for walls that have beams, columns, or joists resting on them.
- Professional Assessment: When in doubt, consulting a structural engineer or a qualified contractor can ensure accurate identification of load-bearing walls.
- Although the load bearing walls are typically perpendicular to the ceiling joists, however, there are cases in which the wall is supporting the loads from the upper floors and this make them to be load bearing. Examples could be the staircase walls, in some cases, as on the main floor are not supporting the ceiling joists, however, they are supporting the second floor load bearing wall.
Due Diligence and Pre-Removal Considerations
- Building Codes and Permits: Before removing a load-bearing wall, it's essential to check local building codes and obtain necessary permits. Compliance with regulations is crucial for safety and legal reasons.
- Structural Analysis: Conduct a thorough structural analysis to determine the load distribution and the impact of wall removal. This may involve calculating the loads that the wall supports and designing an appropriate support system.
- Engineering Provisions: Engage a structural engineer to design a replacement support system. This often involves specifying beams, columns, and other structural elements that can safely redistribute the loads.
Engineering Solutions and Beam Selection
- Beam Types: The type of beam chosen depends on the span of the removed wall, the load it supports, and the overall structural design. Common types of beams include:
- Steel Beams (I-Beams): Known for their strength and durability, suitable for long spans and heavy loads.
- Laminated Veneer Lumber (LVL) Beams: Engineered wood beams that offer high strength and consistency.
- Glulam Beams: Made from glued layers of timber, these beams are strong and aesthetically pleasing.
- Support Columns: In addition to beams, vertical support columns may be required to transfer the load to the foundation. These can be made of wood, steel, or a combination of materials.
- As per the Ontario Building Code, and as for any span to 4.9m (16 ft length of the load bearing wall) the alternative beam could be selected from the span tables available in the code (tables A1 to A37 Section 9.40.2.2.); any span beyond the table limits has to be designed by an Engineer.
Considerations and Process
- Temporary Support: Before removing the load-bearing wall, install temporary supports to hold the weight during construction. This typically involves building a temporary wall or using adjustable steel columns (jack posts).
- Removing the Wall: Carefully demolish the load-bearing wall while ensuring that the temporary supports remain in place and stable. Proper tools and safety equipment should be used to avoid accidents.
- Installing the Beam: Position the new beam in place, ensuring it is level and properly supported at both ends. This may involve creating pockets in the existing walls or adding new support columns.
- Transferring the Load: Gradually transfer the load from the temporary supports to the new beam. This should be done slowly and methodically to prevent sudden shifts or structural damage.
- Finishing Touches: Once the beam is securely in place, remove the temporary supports and make any necessary adjustments. Finish the surrounding area to match the existing construction, including drywall, trim, and paint.
Conclusion
Removing a load-bearing wall in a wood frame structure is a complex process that requires careful planning, expert knowledge, and adherence to building codes and engineering principles. By accurately identifying load-bearing walls, performing due diligence, and implementing the correct engineering solutions, homeowners and contractors can safely and effectively modify their living spaces. Always consult with professionals to ensure the structural integrity and safety of the building during and after the renovation.